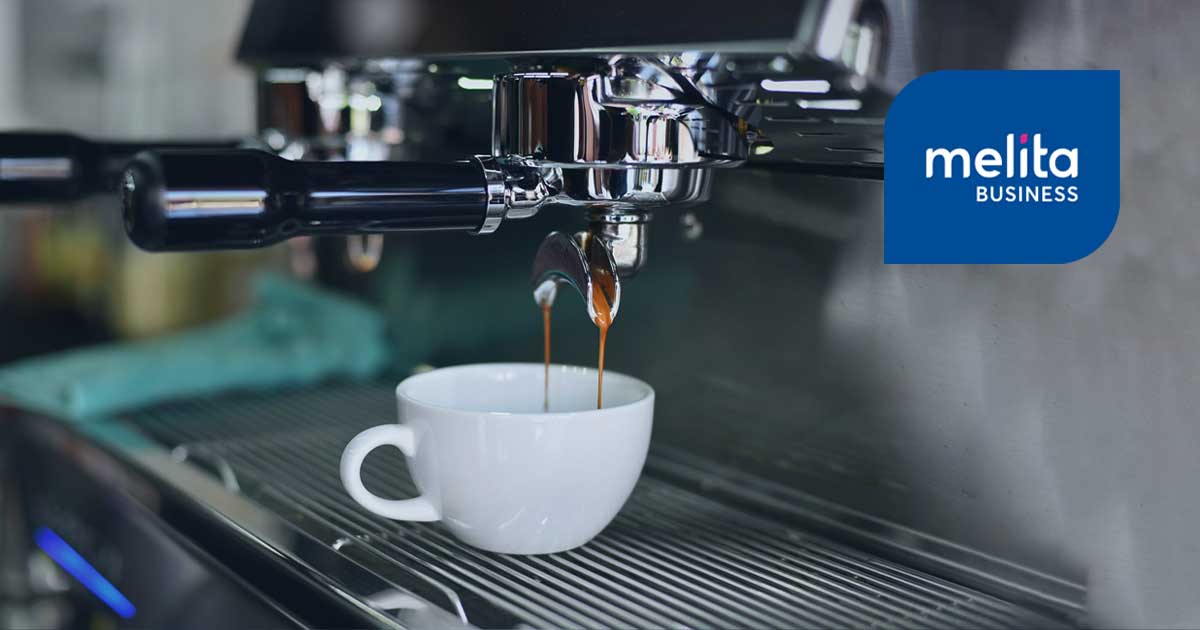
The smell of good coffee is hard to resist, and the industry is bustling with high quality coffee brands, all fighting for their share of the market.
Coffee companies are very proud of their brands and often offer their clients such as bars, restaurants and other catering establishments, sophisticated coffee machines for free.
As part of this business agreement, catering establishments agree to use the company’s coffee brands exclusively, and to manage the machine’s daily maintenance as instructed by the company.
On the other hand, the coffee company agrees to maintain the coffee machine regularly and as necessary.
However, both parties sometimes find it challenging to stick to their end of the bargain with the main issues stemming mostly from a logistical base.
Melita through its IoT connectivity solution and technology partners is helping to address the top three challenges faced by coffee companies and catering establishments:
- Brand Loyalty: Making sure that the catering establishments use the coffee brand they have agreed to use whilst ensuring timely supply
- Maintenance Costs: Making sure that the coffee machines are operated and cleaned appropriately. (E.g. daily proper cleaning of the wand and controlling the correct temperature settings).
- Efficiency: Helping the coffee companies manage the logistics of maintaining many machines in different establishments across the country.
On a technical level, and this is where the real fun begins; coffee companies are looking at the possibility to fit the coffee machines with smart IoT sensors that would remotely communicate information to a central data hub. This real-time data is sent through a gateway via Melita’s mobile connection, and after being filtered through the coffee companies’ analytics software, the company’s management would be able take quick and informed business decisions, activate maintenance plans, and deploy maintenance works as necessary.
With the sensors communicating in real-time with the analytics software, the coffee machines turn into smart machines that can control various functionalities. These would include power management and the ability to switch the machine on and off remotely, boiler and pump control, which in the long run avoids damage to the machine, and also alerts to indicate the need for cleaning or purging different parts of the machine. The data will also be able to capture the amount of coffee served over a period of time, which when matched to the amount of coffee bought, would automatically highlight any discrepancies – the coffee company can then follow up with the café owner, and check if other coffee brands are being used in their coffee machine.
This IoT solution will not only ensure the right coffee is being used; it will reduce the need for machine repairs, and enable better planning of any ad-hoc or planned maintenance, reducing damage losses and increasing operational efficiency. It will also result in a more streamlined and consolidated operational strategy, a reduction in operational costs, more efficient safety and compliance checks, and ultimately, what every good businessperson is after – better customer satisfaction for all the coffee lovers out there